Foam Conversion and Bespoke Acoustic Solutions: An Overview
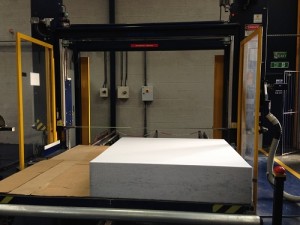
Introduction to Foam Conversion
Foam conversion is a specialized process of transforming raw foam materials into tailored products that meet specific requirements. This versatile technique involves modifying foam into various shapes, sizes, or forms for diverse applications. By utilizing advanced methods like slitting, CNC profiling, and laminating, foam conversion enables the creation of bespoke acoustics and other customized solutions across industries.
In this article, we’ll delve into the benefits, processes, applications, and advantages of foam conversion while highlighting its importance in creating bespoke acoustic solutions.
What is Foam Conversion?
Foam conversion transforms raw foam materials such as polyurethane, polystyrene, or polyethylene into customized products tailored to industry-specific needs. This involves processes like cutting, molding, and laminating to deliver a product that meets functionality, design, and performance criteria.
At Acoustafoam, foam conversion is enhanced with advanced equipment, including:
- Band saws
- CNC profiling machines
- Laminators
- Die-cut presses
- Spray booths
- Water jets
These tools enable precise modifications, ensuring the foam is optimized for applications ranging from sound absorption to thermal insulation.
Applications of Foam Conversion
Foam conversion plays a critical role in various industries, offering tailored solutions to meet specific challenges. Below are some primary applications:
1. Acoustic Solutions
Foam conversion is integral in creating bespoke acoustics for soundproofing and sound absorption. Acoustic foam, crafted through this process, reduces echoes, reverberations, and noise levels in environments like recording studios, home theaters, and offices.
2. Packaging
Customized foam packaging protects delicate items during transit. Foam can be cut and molded to securely house products, ensuring minimal risk of damage.
3. Automotive Components
Foam conversion produces headrests, armrests, and thermal insulation materials for automotive interiors. These components enhance comfort and functionality.
4. Insulation
Foam materials processed through conversion provide excellent thermal and sound insulation, ideal for construction, marine applications, and industrial uses.
5. Medical Equipment
Foam conversion delivers orthopedic supports, cushions, and other healthcare products that require precision and durability.
The Benefits of Foam Conversion
Foam conversion is not just about modifying foam—it’s about creating solutions that cater to specific needs. Some of the key benefits include:
1. Customization
The ability to tailor foam products to precise specifications allows industries to meet unique requirements, such as bespoke acoustics for sound-sensitive environments.
2. Versatility
Foam conversion accommodates various foam types, including:
- Polyurethane Foam: Ideal for cushioning and packaging.
- Polystyrene Foam: Lightweight and effective for insulation.
- Polyethylene Foam: Durable and moisture-resistant.
3. Eco-Friendly Options
Foam conversion processes increasingly incorporate recycled and eco-friendly materials, reducing environmental impact.
4. Cost-Effectiveness
By optimizing foam materials for specific applications, foam conversion minimizes waste and enhances product efficiency.
5. Enhanced Performance
Converted foam products can offer improved acoustic, thermal, and structural properties, making them invaluable in specialized industries.
Bespoke Acoustics: Tailored Soundproofing Solutions
One of the standout applications of foam conversion is bespoke acoustics. This process involves creating custom foam solutions to manage sound within a space effectively.
Features of Bespoke Acoustics
- Sound Absorption: Acoustic foam panels absorb sound waves, reducing noise and echoes.
- Custom Designs: CNC profiling enables precise shaping of foam to meet aesthetic and functional needs.
- Material Flexibility: Acoustic foam can be paired with additional layers, such as polymeric barriers, to enhance soundproofing.
Applications of Bespoke Acoustics
- Recording Studios: Reduce echoes and background noise.
- Home Theaters: Improve sound clarity for a premium audio experience.
- Public Spaces: Control noise levels in gyms, restaurants, and auditoriums.
The Role of Class 0 Foam in Acoustic and Thermal Applications
Class 0 foam is a high-performance material that excels in sound absorption and fire resistance. Treated with a mineral compound, it is non-combustible, making it suitable for high-risk environments.
Key Features of Class 0 Foam
- Fire Resistance: Does not support combustion, ensuring safety in critical applications.
- Flexibility: Easily molds to curved surfaces and complex shapes.
- Acoustic Properties: Exceptional at reducing noise in engine rooms, industrial vehicles, and generator canopies.
Benefits of Class 0 Foam
- Nontoxic and safe to handle.
- Available with self-adhesive backing for easy installation.
- Resistant to erosion and air movement.
Applications include marine environments, high-heat areas, and automotive interiors, where safety and soundproofing are paramount.
Advanced Foam Conversion Processes
Foam conversion involves state-of-the-art techniques to achieve precise results. Below are some key processes:
1. Cutting
Techniques such as water jet and hot wire cutting allow foam to be shaped into intricate designs.
2. Laminating
Combining multiple foam layers or bonding foam to other materials enhances durability and functionality.
3. CNC Profiling
Computer-controlled machines ensure precision, enabling the creation of complex shapes for bespoke acoustics.
4. Die-Cutting
Die presses efficiently cut foam into specific shapes, optimizing the material for mass production.
5. Molding
Injection or compression molding shapes foam into desired forms, ideal for automotive and medical applications.
Quality Control in Foam Conversion
Ensuring quality is critical in foam conversion. Rigorous standards and testing ensure products meet both industry requirements and customer expectations.
Quality Assurance Measures
- Testing for durability, fire resistance, and acoustic properties.
- Precision measurements to achieve accurate dimensions.
- Use of advanced machinery for consistent results.
Foam Conversion in the Future
As industries evolve, foam conversion continues to expand its capabilities. Innovations such as sustainable materials, improved machinery, and enhanced customization options position foam conversion as a key contributor to modern manufacturing.
Moreover, the demand for bespoke acoustics, energy-efficient insulation, and environmentally friendly packaging ensures that foam conversion remains a versatile and valuable process.
Read also: PAT Testing Telford: Ensuring Safety for Your Electrical Systems
Conclusion
Foam conversion is a transformative process that combines advanced techniques with industry expertise to deliver tailored solutions for diverse applications. From bespoke acoustics to automotive components and medical equipment, foam conversion’s versatility makes it an indispensable tool across sectors.
Acoustafoam’s commitment to innovation ensures that every foam product meets the highest standards of quality and performance. Whether for soundproofing, insulation, or packaging, foam conversion offers unmatched customization and efficiency.
For tailored solutions in foam conversion or bespoke acoustics, contact Acoustafoam today. Their expertise will help you achieve optimal results, no matter the challenge.